課題解決事例
新製品のオイルホースに、耐久テストで亀裂が・・・
オイルの添加剤によるダメージに耐えるホースが完成した理由
自動車部品メーカーC社
材料技術部
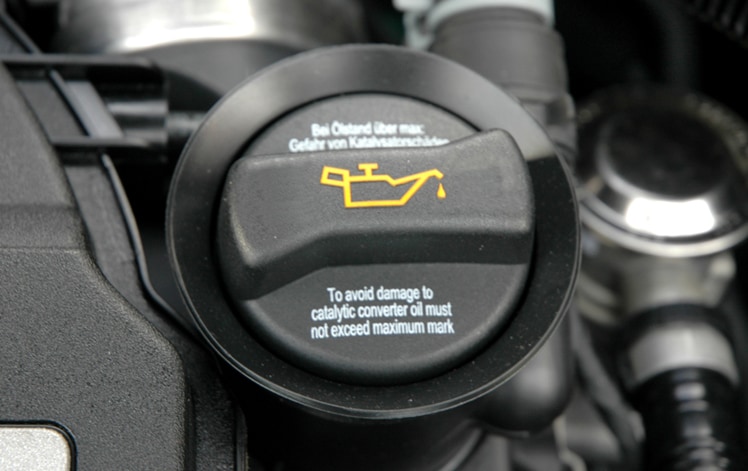
解決
解決のポイント
耐塩基性(耐アミン性)に優れたAGCのフッ素ゴムAFLAS®を知る
AFLAS®の耐塩基性を活かして耐久性基準をクリアできた
重量や硬さの問題も、他素材(アクリルゴム)と「積層」したことでクリアでき、「軽量化」「柔軟性」もアピールできるオイルホースが完成した

耐塩基性に優れたAGCのフッ素ゴムAFLAS®で、耐久性の高いオイルホースが完成
原料に詳しい成型加工メーカーに問い合わせたY氏は、AGCが提供するフッ素ゴムAFLAS®の存在を知り、同社の担当者から詳しい説明を受けることにした。
担当者の話では、AFLAS®は200℃連続使用可能な耐熱性を維持しながら、これまでになく耐塩基性に優れたフッ素ゴムであった。特に、エンジンオイルにさび止めや潤滑性を高める目的で添加されているアミンに対して高い耐性を持っていた。
Y氏は早速AFLAS®のサンプルを取り寄せ、評価を行なうことにした。
「試作品を再度作成して、耐久テストを何度も実施してみましたが、オイルによるホースの劣化や亀裂などのダメージはほとんど見られませんでした。明らかにFKMで製造したものに比べてAFLAS®は優れた性能を持っていることがわかりました。AFLAS®を原料とすれば提示された全ての仕様のオイルホースを開発できると踏みました」(Y氏)
しかしこの後も決して円滑には進んだ訳ではなかった。すぐにAFLAS®を原料にホースを試作して、自動車メーカーに持込んだものの、自動車メーカー側が提示した複数のタイプのうち一部は、そもそもフッ素ゴム単体で成型されたホースでは重量がオーバー、またその硬さによる取回しの悪さにも難色を示されてしまった。
再度AGCに、硬さ・重量について相談したところ、アクリルゴムとの積層化という方法を提案された。AFLAS®の新グレードである400E、600Xは他のゴム素材との相性も良く、積層加工も容易にできるということであった。早速AFLAS®とアクリルゴムを積層加工し、ホースの内側にAFLAS®、外側にアクリルゴムが来るように、試作品を成型、各種の耐久性テストを実施したところ、AFLAS®のみを使った時と殆ど変わらない評価を得ることができた。ホース自体の重量と硬さは許容範囲内に抑えることができ、新型オイルホースの完成が見えた。
ここに至って、「軽量化」「柔軟性」というポイントも前面に打ち出し、これらと耐久性向上を同時に実現することで製品品質を高めることに成功したC社。納入先の自動車メーカーからもこの点を高く評価され、新たな部位の受注を獲得することに成功した。
同社では今後も、AGCからのアドバイスを参考にしつつ、他のホース類についても開発を進めて品質向上を目指していく計画だ。
この課題を解決したソリューション
- 1
2